Achievement advances quest for bionic eye prototype
The act of “seeing” is the result of a complex system of biological tissues that capture and focus light onto an array of photosensitive receptors in the retina that converts light into electrical signals and sends them to the brain through the optical nerve.
Recreating that photosensitive array on a curved surface has been one of the biggest challenges for researchers trying to develop a prosthetic vision device or “bionic” eye that can replicate the experience of vision.
In a significant advance toward that goal, researchers at the University of Minnesota have for the first time fully 3D printed an array of light receptors on a hemispherical surface. The study was published in the August 2018 journal of Advanced Materials.
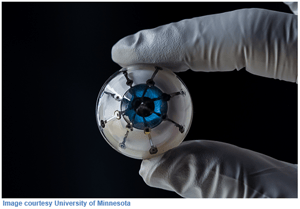
The research group led by Michael McAlpine, PhD and professor of mechanical engineering at the University of Minnesota has also successfully 3D printed a scaffold with live neurons for implanting into the spine as well as successfully using 3D printing to produce “bionic skin,” and a “bionic ear.”
Traditional microfabrication processes based on cleanroom lithography and dry or wet etching processes are essentially two-dimensional methods. Complicated procedures designed to create some three-dimensional microstructures accurately on a curved surface have proven extremely difficult.
Using 3D printing has been adopted as a possible solution, however, one of the challenges of 3D printing on a curved surface has been the tendency of printed materials running down the curved surface.
In this study the researchers developed a custom-built 3D printer that overcomes the challenge of printing electronics on a curved surface using semiconducting polymer materials to print photodiodes, which convert light into electricity. The process takes about an hour.
The resulting 3D printed semiconductors on a curved surface only achieved 25 percent efficiency in converting light into electricity, far from what is needed, but a long way toward showing the process is feasible.
“We have a long way to go to routinely print active electronics reliably,” McAlpine said in a press release, “but our 3D-printed semiconductors are now starting to show that they could potentially rival the efficiency of semiconducting devices fabricated in microfabrication facilities. Plus, we can easily print a semiconducting device on a curved surface, and they can’t.”
The next step in the group’s research is to create a prototype with more light receptors that are even more efficient, and to print on a soft hemispherical material that could one-day be implanted into a real eye.
Kapstone Medical is a full-service product realization firm that partners with inventors and manufacturers of all sizes to rapidly develop and commercialize new medical devices or processes. We love sharing the latest news in 3D printing and what’s going on in the MedTech Industry. For more information contact us today at (704) 843-7852 – or by email at info@kapstonemedical.com.
Sources: Advanced Materials journal, https://doi.org/10.1002/adma.201803980 and University of Minnesota press release